Common Rivet Materials: Aluminum, Carbon Steel, Stainless Steel, and Copper
Overview
Rivets are commonly used fasteners in various industries, and the material of the rivet is critical in determining its performance, strength, and resistance to corrosion. The most common materials for rivets include aluminum, carbon steel, stainless steel, and copper. Each material offers unique properties that make it suitable for different applications. In this article, we will explore these four common rivet materials, their characteristics, and typical uses.
1. Aluminum Rivets
Summary: Aluminum rivets are lightweight and resistant to corrosion, making them ideal for applications where weight is a critical factor.
Content: Aluminum rivets are known for their lightness and excellent corrosion resistance, making them popular in industries such as aerospace, automotive, and electronics. The natural oxidation of aluminum creates a protective layer that ensures durability, even in humid environments. Aluminum rivets are also easy to install due to the softness of the material. However, they are not as strong as carbon steel or stainless steel rivets, so they are typically used in applications with lower stress requirements.
Typical Uses: Aircraft construction, automotive panels, electronic device casings.
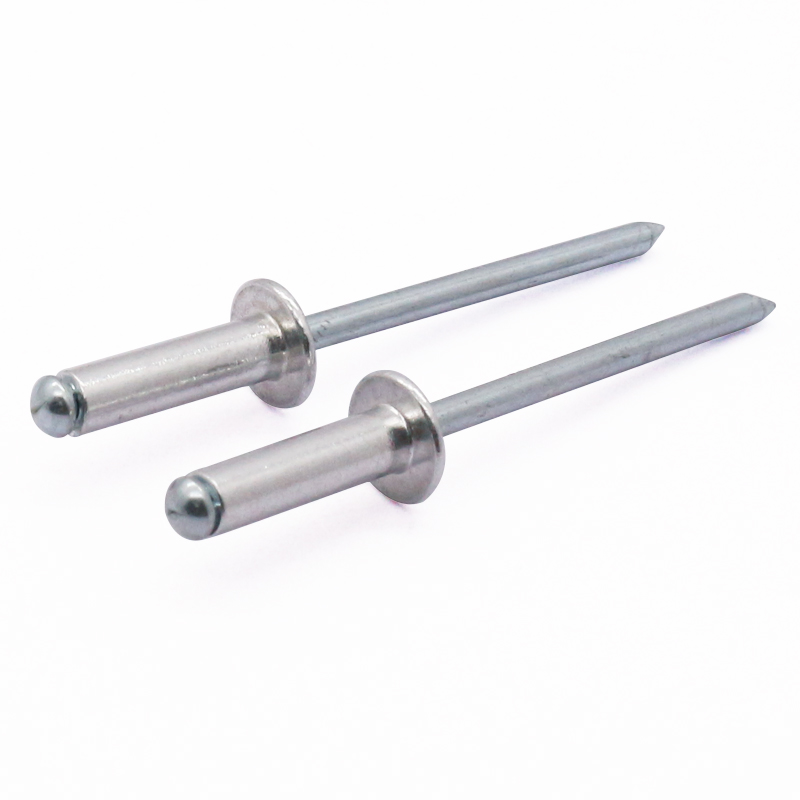
2. Carbon Steel Rivets
Summary: Carbon steel rivets offer high strength and are cost-effective, but they require coatings or treatments to prevent rust in corrosive environments.
Content: Carbon steel rivets are widely used in construction, machinery, and structural applications due to their high tensile strength and durability. Carbon steel is stronger than aluminum, making these rivets ideal for heavy-duty applications that require greater load-bearing capacity. However, carbon steel is prone to rust when exposed to moisture or corrosive environments. To prevent corrosion, carbon steel rivets are often galvanized or coated with protective materials like zinc. These treatments allow carbon steel rivets to be used in environments where direct exposure to harsh conditions is minimized.
Typical Uses: Structural steelwork, heavy machinery, general industrial applications.
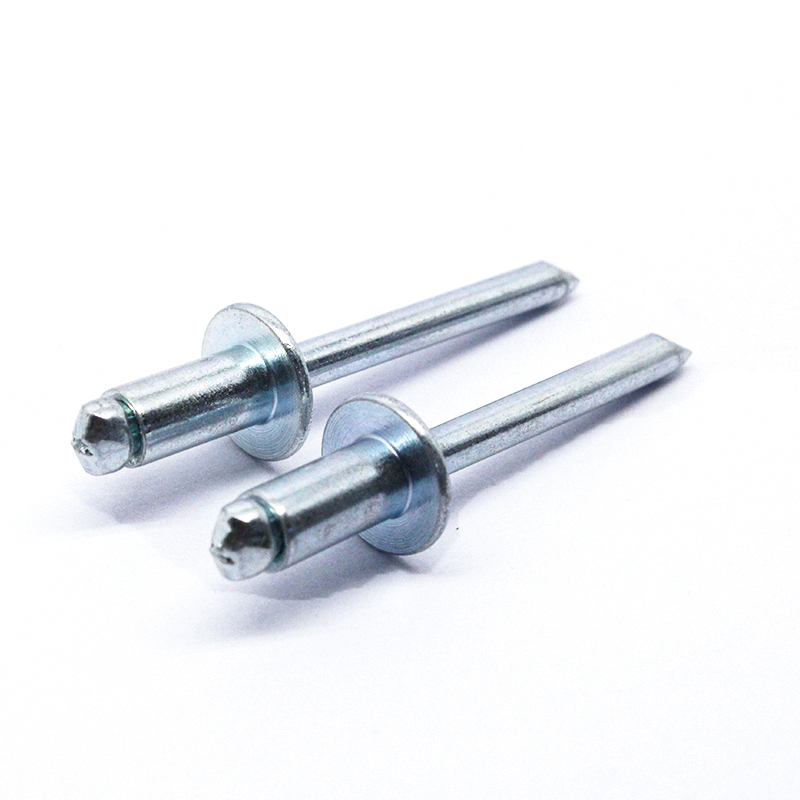
3. Stainless Steel Rivets
Summary: Stainless steel rivets provide superior corrosion resistance and strength, making them suitable for harsh environments.
Content: Stainless steel rivets are known for their excellent resistance to corrosion and rust, making them the go-to choice for applications exposed to moisture, chemicals, or saltwater. In addition to their corrosion resistance, stainless steel rivets are also incredibly strong and durable, capable of withstanding extreme conditions over long periods. While they are harder to install due to the material's hardness, they are widely used in industries like food processing, outdoor construction, and medical equipment where both hygiene and long-term durability are essential.
Typical Uses: Outdoor structures, food processing equipment, chemical and medical devices.
4. Copper Rivets
Summary: Copper rivets offer excellent electrical conductivity and corrosion resistance, making them suitable for electrical and decorative applications.
Content: Copper rivets are commonly used in electrical systems due to their superior conductivity. They are also resistant to corrosion, especially in marine and humid environments, making them a great choice for applications that are exposed to saltwater. Copper is a softer metal, which makes these rivets easy to install and work with in applications that require flexibility. Additionally, the warm appearance of copper rivets makes them popular for decorative purposes, though they are not as strong as carbon steel or stainless steel rivets.
Typical Uses: Electrical equipment, marine engineering, decorative hardware, furniture assembly.
Conclusion
Selecting the right rivet material depends on the specific requirements of the application, such as strength, weight, corrosion resistance, and cost. Aluminum rivets are ideal for lightweight and corrosion-resistant applications, while carbon steel rivets provide high strength at a lower cost but need corrosion protection. Stainless steel rivets offer the best performance in harsh environments due to their superior corrosion resistance and strength. Lastly, copper rivets are perfect for applications requiring electrical conductivity or a decorative finish. Choosing the appropriate rivet material ensures the strength, durability, and longevity of the fastened joints.